… sang Oasis in their 1995 song of the same name. But right now, a quarter of a century on, the construction industry is still very much diesel-powered.
As the quest for a greener future continues, here at WJ we want to make sure we’re doing our bit as we look to help move the industry forward to a more sustainable approach.
The construction emissions struggle
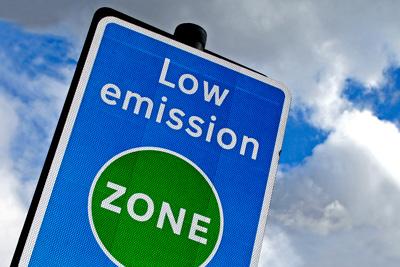
According to the Centre for Low Emission Construction, the construction industry is estimated to contribute 7%, 34% and 15% respectively to NOX, PM10 and PM2.5 emissions within London (LAEI 2106). And across the capital, in regional bodies and in nationwide strategies, construction emissions are increasingly becoming important factors in developing air quality policies.
Across the globe, around 200,000 people are migrating to urban areas every single day, driving up the requirement for affordable housing and supporting infrastructure. The construction industry meets this demand, but with consequential impacts on emissions and air quality. This urban migration is only set to increase, and as a result requires further quantification and regulation by local and national governments… but also a forward-thinking approach by those operating within the industry around how to contribute in a more environmentally friendly way.
Protecting workers
It’s unsurprising that construction workers are exposed to the greatest levels of risk due to their proximity on site to machines and activities that produce pollution.
“During the 2016/17 period around 3000 construction workers were suffering with breathing and lung problems”
CITB
The CITB has reported that during 2016-2017 around 3000 construction workers in the UK were suffering with breathing and lung problems that they believed had been caused by or made worse as a result of their work. As employers, we have a duty of care for our staff, and should strive to reduce or remove any unnecessary risk to them. This should include giving them the safest possible tools to carry out their work.
Meeting regulatory compliance
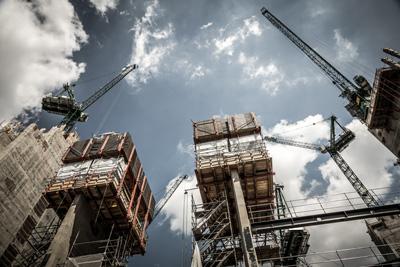
The implementation of the London congestion charge and a national strategy based around higher taxes for more polluting vehicles has encouraged in recent years a significant fall in the harmful emissions from transport, but construction still largely relies on diesel engines powering everything from the 8kw pressure washer cleaning tyres at the site gates, to the 200 tonne, 800 kw diaphragm wall machine building the foundations. Many of these machines, particularly the older equipment, is powered by highly polluting diesel engines.
The recent establishment of London’s Ultra Low Emission Zones (ULEZ) requires that from 1 September 2020 Non Road Mobile Machinery (NRMM) used on any site within Greater London will be required to meet Stage IIIB of the Directive as a minimum. NRMM used on any site within the Central Activity Zone or Canary Wharf will be required to meet Stage IV of the Directive as a minimum. So slowly, construction plant is being forced to clean up its act, but remains some way behind the cleanest diesel engines currently available for trucks and buses.
WJ’s electrifying moment
WJ has always had a policy of purchasing the cleanest diesel engines possible, not only for compliance, but also to minimise the risk of harm to our employees, and the population of London and other big cities. All of WJ’s drilling machinery is at least Stage 4f. But when we recently needed to invest in new drilling rigs and pumps we asked the question – instead of playing catch up with Stage 4f or Stage 5 or 6 diesel engines, why don’t we get rid of them altogether and use electric motors?
“Instead of playing catch up with… diesel engines, why don’t we get rid of them altogether and use electric motors?”
Historically, the challenge to using electric plant is providing the infrastructure to support such equipment and the benefit of lower particulates and NOX emissions is reduced if the electricity has to be generated by a diesel fuelled generator. However, many of our projects are tunnelling related where installing substations and electrical distribution is required in any case for tunnelling equipment and for urban sites, increasingly a pre-commencement condition will be having a suitable electric supply in place. Electric mini excavators, telehandlers and piling rigs are now available.
Benefits beyond emissions
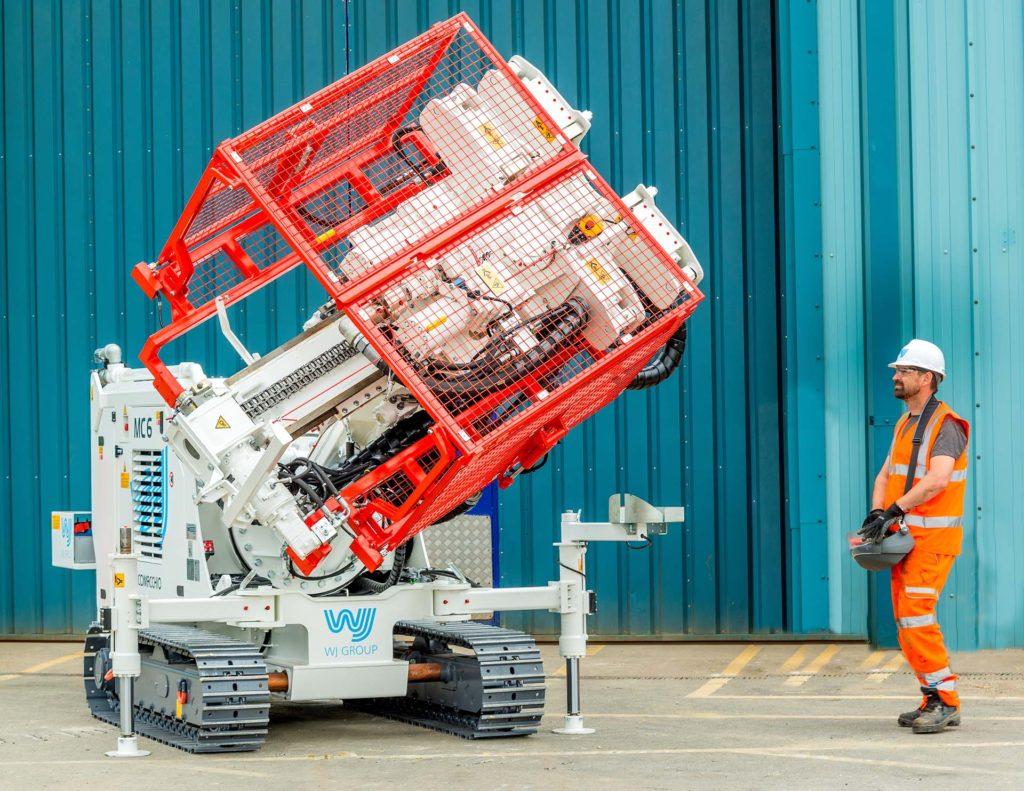
Of course, there are other advantages to using electric powered plant, particularly when working with water – the reduced risk of polluting water courses or the ground with accidental spills of fuel or lubricating oil, better reliability, higher efficiency, less downtime for servicing, no waste oil or filters and reduced noise emissions.
Plus, WJ has had 30 years of experience of safely controlling and distributing high voltages around construction sites for large dewatering systems. We put this experience to use to design and build the electric power distribution and controls which are quick and safe for our staff to set up and secure from accidental damaged caused by construction site activities.
The first step
While we’ve advocated the use of the most efficient diesel engines for years, this is WJ’s first big step into going electric. We recognise that the industry has a way to come to support a greener, more sustainable future and we’re proud to be part of the solution. And to return to how we started this article with Oasis and their 90’s britpop, as long as we’re making strives to a more environmentally friendly future, we’ll happily roll with it.
You can find out more about our fantastic new electric kit and download spec sheets on the electric dewatering kit webpage.
Join the conversation